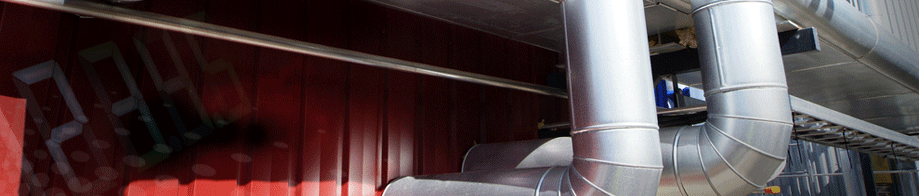
CASE HISTORY
Engineering Case Studies
KBD Technic is an Industrial Ventilation Engineering firm with divisions dedicated to system design, stack testing and system analysis. We have had projects in 35 states and foreign countries. The following is a representative listing of the type of projects we have completed for a broad base of clientele.
Engineered and provided construction bid package for the installation of pollution control system at a secondary brass melting and fabrication facility in the Middle East. Equipment consisted of a 400 HP Scrubber system ( P=50″) and 90,000 CFM baghouse. Including coordination of all purchase agreements with equipment vendors.
Designed complete ventilation system to duct VOC’s and odors from 30 process mixing vessels to a thermal incinerator for a large mid-western chemical manufacturer. Provided complete double line construction drawings and specifications.
Provided conceptual design and cost justification for convective cooling system for steel tubing fabrication line, including specification of air volumes, static pressures, plenum designs and horsepower requirements.
Engineered and provided construction bid package for the installation of arsenic abatement (44,000 ACFM @ 660øF.) in a glass manufacturing facility. Project included the design of a twelve foot diameter, ninety foot tall spray cooler and connection to present baghouse system.
Evaluated the ventilation system and VOC emission control system of a lost foam process at a large automotive foundry with the objective of reducing plant operating costs. KBD Engineers evaluated the existing systems and researched alternative operating strategies and control technologies. Four operating scenarios were developed and the capital costs, operating costs, and return on investment for each were developed and presented to plant management.
Conducted ventilation survey for Fortune 100 Company at seven plant locations in United States and Canada. Provided on-site verification of all system flow rates and made recommendations for system improvements and estimated construction costs.
Designed and specified ductwork, controls and equipment for the installation of a 40,000 CFM lead dust control system and connected HVAC system to ensure proper air balance and minimal leakage to work environment. Met 50 g/m3 OSHA standards and strict humidity controls for process.
Provided complete system analysis for a Fortune 50 aluminum processing facility to bring present control equipment into compliance with state regulations. Included redesign of hoods and ductwork to allow use of present fan and 400 HP motor as well as alterations to baghouse dust collector to reduce maintenance and improve performance.
Designed and specified equipment for asphalt coater ventilation system collecting tars and other hydrocarbons. Project included design of special collection system and hoods and project management of installation.
Designed asbestos dust control system for large automotive parts making facility in the Midwest. Included re-use of present baghouse collectors and fans and static design of system ductwork (no blast gates or orifice plates).
Designed scrubber and duct system for the control of sand and resins from large steel foundry including specification of new medium energy scrubber unit after providing bid evaluation of alternative control strategies.
Performed extensive ventilation engineering study for automobile manufacturer which included airflow measurement and documentation of 260 exhaust stacks and 100 replacement air systems. The study evaluated all plant air flows with an emphasis on positive and negative pressure areas within the work spaces.
Engineered and provided construction bid package for oil mist control systems on several automotive transfer lines at Midwestern transmission plant including machines furnished by Lamb, Kingsbury and others. Project included specification and design of all hoods, ductwork and oil mist collection devices. Drawings were completed to shop quality detail for fabrication by plant’s maintenance department.
Provided complete system analysis and recommendations for large brass foundry to bring present dust collection equipment and ductwork system into compliance with present codes and prepare for effects of 1990 Clean Air Act Amendments.
Provided RACT study for vinyl coating facility in the Midwest to meet requirements of local regulatory authority.
Stack Testing Case Studies
Determined the capture efficiency and destruction and removal efficiency of 15 automotive paint systems as required by the National Emission Standards for Hazardous Air Pollutants: Surface Coating of Automobiles and Light-Duty Trucks. USEPA Methods 25A, 204B and 204D were used. Multiple sites were sampled simultaneously to determine the capture efficiency and destruction and removal efficiency of the paint systems.
- Determined capture efficiency of eight small parts paint lines using USEPA Methods 204B, 204D and 204F. Multiple sites were sampled simultaneously to determine captured and uncaptured emissions. Data was used to demonstrate compliance to various Federal and State Agencies.
- Routinely test VOC abatement systems in automotive assembly plants for control system efficiency. Equipment tested includes carbon adsorption systems, regenerative thermal oxidizers, and catalytic oxidizers.
- Verified that a room enclosure met the requirements of a Permanent Total Enclosure (PTE) using USEPA Method 204. Conducted tests on the emission control system using Methods 25 and 25A to determine system control efficiency as a condition for a Permit To Operate.
- Conducted tests on several engine test cell dynamometer incinerators for NOx, CO and VOC.
- Conduct annual RATA tests on two continuous hydrocarbon analyzers that monitor VOC emissions on a solvent recovery system at a paper coating facility.
- Designed Temporary Total Enclosures for surface coating operations. TTE’s met Method 204 criteria and were used to determine VOC capture efficiency.
- Conducted emission tests at several automotive assembly plants on paint booth VOC concentrators and incinerators. Continuous measurements using USEPA Method 25A were made to determine the VOC emission rates and destruction efficiency. The data is electronically logged and displayed for real time test results. The test data is used for a compliance demonstration for various state agencies.
- Conducted stack tests on utility boiler firing pulverized coal for emissions of particulate matter, nitrogen oxides and sulfur dioxide using USEPA Methods 1-5, 7e, and 8. The test data was used to demonstrate compliance with the state regulatory agency.
- Sampled pilot scale bio-filtration VOC removal system to determine the VOC removal efficiency. The system treats a slipstream of solvent laden air from a painting operation.
- Conducted stack tests on chrome plating operations for emissions of total chromium. Chromium emissions were determined using the USEPA Method 306 train.
- Sampled VOC emissions from printing presses and the associated pollution control system using Methods 25 and 25A.
- Conducted compliance tests on two glass smelters. The smelters were tested for particulate matter, nitrogen oxides and hydrogen fluoride.
- Conducted stack tests on several sources at an automotive engine and transmission assembly plant for low level particulate emissions. Six-hour test runs were made on several sources.
- Sampled VOC emissions from printing presses and the associated pollution control system using a Methods 25 and 25A sampling train for a compliance demonstration for the Ohio EPA.
- Conducted emission tests at an engine manufacturing plant in Ohio. Ten sources were tested for total particulate emissions and PM10 emissions. The PM10 samples were collected using USEPA Reference Method 201A.